Smarte IoT-Lösungen mit CANopen im Edge Controller
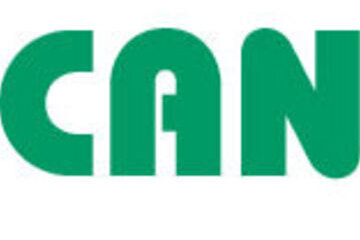
IoT verfolgt den Ansatz, neue Technologien und Kommunikationskonzepte zu nutzen, um Daten in einer Cloud verfügbar zu machen, diese zu verknüpfen und weiteren Nutzen aus diesen Daten zu generieren. Am verbreitetsten sind hier die Datenübertragung via MQTT oder die Anbindung von Daten an die Cloud mittels OPC UA. Aktuelle Entwicklungen gehen noch einen Schritt weiter und betrachten das Edge Computing als Möglichkeit der Automation und Vernetzung von Prozessen am Ort des Geschehens, also dort wo Daten generiert werden – in der industriellen Produktion, direkt an der Maschine.
Warum, mit welchen Mitteln und Methoden lohnt es sich noch einen Schritt weiter zu gehen? Sollte IoT direkt in das Gerät, in einen Maschinenteil oder unmittelbar in die Sensorik und Aktorik integriert werden? Diese Fragen beantworten Dr. Frank Jungandreas, Senior-Ingenieur bei der SYS TEC electronic AG und Nadine Mensdorf, Produktmanagerin bei der SYS TEC electronic AG.
Wo ordnen Sie CANopen ein? Was verbindet SYS TEC electronic mit CANopen?
Nadine Mensdorf: CANopen hat sich schon seit längerer Zeit als Ersatz für proprietäre Backplane-Busse innerhalb von Geräten etabliert. Auf dem Markt findet man CANopen beispielsweise in Sondermaschinen, in Batteriemanagementsystemen, Nutzfahrzeugen, im Lift- sowie im Mobilitätssektor. Konkret verbindet es Sensorik und Aktorik in einer Maschine und überträgt Statuswerte sowie Prozessdaten oder löst andere Aktionen aus. So wie CAN in der Automobilbranche verwendet wird, wird CANopen bei Spezialfahrzeugaufbauten, wie Feuerwehrwagen, Kränen oder Landmaschinen eingesetzt.
Unseren CANopen Stack haben wir sowie auch unsere Kunden über viele Jahre für diverse Controller und Endgeräte in unterschiedlichsten Applikationen portiert. Zahlreiche kundenspezifische Entwicklungen und gefertigte Produkte beinhalten unsere Lösung. Auch in aktuellen Anfragen und Projekten, sowie Kundenlösungen setzen wir CANopen ein. Zu unserem Produktportfolio gehören unser CANopen Chip, die auf ihm basierenden sysWORXX I/O-Module, sowie unsere industriellen Steuerungen. Wir bieten Endgeräte zum Einsatz auf der Hutschiene, Embedded Control Units, sowie kundenspezifische Individuallösungen. Neben vielen weiteren Protokollen wird unsere CANopen-Implementierung auf allen unseren IoT-Controllern mit IEC 61131-3 SPS-Programmiersystem zur Kommunikation in der Feldebene eingesetzt. Dies gilt für den Edge-Controller sysWORXX CTR-700 ebenso wie für die Single-Chip IoT-Steuerung sysWORXX CTR-100.
CANopen und IoT - wie passt das zusammen?
Dr. Frank Jungandreas: Der IoT-Gedanke wird oft initial mit der Verknüpfung von Daten und Cloud sowie der Anbindung von Geräten an die Cloud durch Protokolle wie MQTT oder OPC UA erklärt. Wie kommt man aber effektiv an bereinigte, vorverarbeitete, für die Auswertung relevante Daten? Betrachtet man eine Anlage im Ganzen, können die Daten oft direkt über deren Steuerung an die Cloud geliefert werden. Damit sind wir inhaltlich schon beim Edge Computing, also der dezentralen Datenaufnahme und -verarbeitung, kombiniert mit der Gateway-Funktionalität, die als Schnittstelle zu übergeordneten Systemen dient.
Eine Maschine im Investitionsgüterbereich als ein in sich geschlossenes Objekt ist nach diesem Ansatz noch sehr großteilig betrachtet. Intern vereint diese doch in ihrer Funktionalität mehrere ausführende und überwachende Geräte, Sensorik und Aktorik. Die Intelligenz für das Internet der Dinge muss dort beginnen, wo sich die „Dinge“ befinden – also genau dort wo Daten generiert werden: nämlich in den Prozessen der industriellen Produktion, also direkt in der Maschine. Betrachten wir die „Dinge“ feingranular als Maschinenteile dedizierter Funktionalität, so muss man damit beginnen, die Objekte in der Maschine mit Intelligenz zu versehen und miteinander zu verknüpfen.
Auf der Ebene zur Vernetzung von einzelnen Maschinen in einer industriellen Produktion herrschen ganz klar Ethernet-basierte Technologien vor. Alle Objekte sind darüber vernetzt. Im Gegensatz dazu kommt diese Technologie innerhalb einer Maschine auf der Feldbusebene jedoch kaum zum Tragen. Die Gründe dafür, warum es innerhalb einer Maschine oft sinnvoller ist auf CANopen zu setzen, statt IP-basierte Technologien zu nutzen, sind vielfältig. Zum einen haben die allermeisten Microcontroller, die heute in Maschinensteuerungen zum Einsatz kommen, bereits eine oder mehrere CAN-Schnittstellen integriert. Die Übertragung von Daten via CAN erfordert signifikant weniger Energie als Ethernet-basierte Systeme und für Inbetriebnahme und Fehlerdiagnose existieren am Markt zahlreiche, kostengünstige Tools.
Wie leistungsfähig CAN ist, lässt sich gut am Beispiel der Automobilindustrie verdeutlichen. Innerhalb des Fahrzeuges wird mittels CAN die Kommunikation der Status von diversen Komponenten realisiert, es werden Prozessdaten übermittelt und Aktionen ausgelöst. Zugleich bietet CAN aber die Serviceschnittstelle nach außen, über die sich Fehlerinformationen und Telemetriedaten auslesen lassen. CANopen bietet im Automatisierungsbereich ebenso viele Vorteile zur Nutzung innerhalb einer Maschine. Schlanke, energieeffiziente Kommunikationseinheiten können mit kostengünstig verfügbarer
CANopen wandert demnach direkt in die Maschinen? Bitte erläutern Sie dies genauer.
Dr. Frank Jungandreas: Genau, viele Maschinen und Geräte verwenden CANopen als internen Maschinenbus, ohne dass dies nach außen sichtbar ist. CANopen ist deutlich schlanker, kleiner und dabei noch kostengünstiger als eine vergleichbare IP-basierte Kommunikation. Hinzu kommt, dass die Verlustleistung ebenfalls deutlich niedriger ist, als beispielsweise bei Ethernet. Somit ist CANopen ideal für autonome, z. B. batteriebetriebene Geräte geeignet. Die Anwendungen in diesem Bereich werden in den nächsten Jahren noch stark zunehmen.
Ein weiteres Einsatzgebiet für CANopen ist Condition Monitoring und Predictive Maintenance, also die ständige Überwachung der Gerätedaten, um mögliche Ausfälle frühzeitig zu erkennen und vorausschauend zu warten. Aufgrund der integrierten CAN-Schnittstellen, der einfachen Verkabelung und des niedrigen Energie- und Rechenleistungsbedarfes kann CANopen in jede beliebige Stelle in einer Maschine mit geringem Aufwand integriert werden. Für unsere Kunden ist auf dieser Basis eine schnelle und günstige Realisierung intelligenter „Dinge“ möglich. Die daraus resultierende Zeit- und Geldinvestition bleibt überschaubar und das technologische Risiko ist gering. Ebenso sind etablierte Unterstützungstools vorhanden, beispielsweise zur Diagnose oder Konfiguration.
Wie sieht ein konkretes Anwendungsbeispiel für dieses Szenario aus?
Nadine Mensdorf: Innerhalb einer Anlage oder Maschine arbeiten mehrere Geräte, die miteinander synchronisiert werden müssen. Die einzelnen Aktuatoren sind voneinander abhängig. Um eine erfolgreiche Kooperation zu gewährleisten, müssen die Geräte untereinander Informationen über ihre Prozesswerte wie Verfügbarkeit, Strombedarf und Wartungsdaten austauschen können. Im Bereich des Energiemanagements können beispielsweise Stromspitzen so verteilt werden, dass Großverbraucher erst nacheinander, statt zeitgleich eingeschaltet werden, um somit die momentane Last der Anlage deutlich zu reduzieren.
CANopen verbindet Sensoren und Aktuatoren zielgerichtet, es überträgt Statuswerte, Prozessdaten und löst Aktionen aus. Es darf keine losgelöste Kommunikationseinheit geben. Vielmehr muss diese direkt in die intelligenten Sensoren und Aktuatoren integriert werden. Ist ein Sensor beispielsweise betriebsbereit, überhitzt oder verschmutzt? Welchen Prozess beeinflusst die Verfügbarkeit des Sensors? Kann ein anderer Sensor die Aufgabe übernehmen oder müssen die Prozesswerte des Gesamtsystems, wie Drehzahl etc., in diesem Fall angepasst werden?
Derart intelligente Baugruppen sind ein Muss für neue Maschinen und Anlagen, bilden sie doch die Basis für Predictive Maintenance. Ein in der produzierenden Industrie sichtbarer Trend geht zum Retrofitting, dem Nachrüsten intelligenter Baugruppen in Bestandsanlagen. Für die Maschinenhersteller eröffnet dies neue Geschäftsfelder, für die Anwender erweitert sich die Investitionssicherheit – auch bei Bestandsanlagen. Maschinenhersteller im Bereich des Sondermaschinenbaus, die sich momentan als Nachzügler sehen, beginnen ihre Maschinenkonzepte um intelligente Baugruppen zu ergänzen. Sensorik- und Aktorik-Hersteller designen die Intelligenz direkt in ihre Geräte ein – diese wiederum dienen als Supplement für Bestandsanlagen.
Sehen Sie Retrofit Lösungen verstärkt am Markt in den kommenden Jahren?
Nadine Mensdorf: Natürlich. Je größer die Investitionen in Maschinen sind, desto länger werden diese typischerweise genutzt. In diesen Bereichen wird der Bedarf zusätzlicher Intelligenz noch wachsen. Eine solche Retrofit-Lösung muss immer in ihrer Gesamtheit betrachtet werden. Erinnern wir uns an die Eckdaten und Vorteile von CANopen. Intelligente, CANopen-fähige Devices lassen sich zu geringen Hardware-Kosten in kurzer Zeit entwickeln. Die Komponenten besitzen eine hohe technologische Reife und bringen so ein geringes technisches Risiko mit sich – aber auch ein hohes Potenzial, neue Geschäftszweige zu generieren.
Zunehmender Leistungs- und Kostendruck fordern eine schnelle Reaktion sowie eine vorausschauende statt reaktionärer Wartung um Einsparungen zu generieren. Der Einsatz innovativer Technologien findet nicht um ihrer selbst willen statt, sondern zur Steigerung der Effizienz. Im Fokus steht hierbei die Aufdeckung versteckter Kosten. Können diese sichtbar gemacht werden, ist es möglich die Probleme zu beheben und Kosten zu senken.
Wie einfach ein intelligentes CANopen Device realisiert werden kann, lässt sich in wenigen Zügen darstellen. Nehmen wir als erstes Beispiel unseren CANopen Chip. Mit diesem Aufsteckmodul können analoge und digitale Werte in sieben verfügbaren I/O-Konfigurationen eingelesen und ausgegeben werden. Das Geräteprofil für CANopen I/O Devices sowie das CANopen Kommunikationsprofil, also die Semantik der Einheit, sind Bestandteil des CANopen Chip. Durch Integration des CANopen Chips in eine Steuerungskomponente kann diese ihre Prozessdaten bereits semantisch definiert mitteilen.
Gehen wir in einem zweiten Beispiel von unserer Single Chip Steuerung, dem sysWORXX CTR-100, aus. In einem intelligenten Maschinenteil benötigen wir lediglich eine simple I/O Anschaltung und den CAN-Transceiver für die Kommunikation. Die gesamte notwendige Intelligenz, um Prozessdaten über CANopen einzulesen, lokal zu verarbeiten und über MQTT an eine Cloud weiterzugeben, ist bereits im Chip des sysWORXX CTR-100 enthalten.
Integriert in einen Sensor, verfügt dieser über Selbstdiagnosefunktionen – er kann selbst erzeugte Werte und Daten sowie Umgebungsdaten verarbeiten, via CANopen steuern, rückwirken auf funktional benachbarte Einheiten, aber auch vorverarbeitete Werte via MQTT an einen übergeordneten Edge-Controller pushen. Die Datenverarbeitung rutscht immer mehr in die Edge, also unmittelbar in die Maschine im Shop Floor - und damit natürlich hinein in die „Dinge“. Nur durch die zielgerichtete Vernetzung der einzelnen „Dinge“ können nutzbringende Daten generiert werden. Eine Cloud allein reicht nicht aus – die Applikation wird erst dann zu einem Geschäftsmodell, wenn sie mit entsprechenden Daten gefüttert und diese verknüpft werden.
Mit dem Edge-Controller sysWORXX CTR-700 lassen sich Daten über CANopen direkt aus der Feldebene aufnehmen und lokal vorverarbeiten. Anschließend können diese Informationen via MQTT oder OPC UA weitergeleitet und so direkt in eine Cloud übertragen werden. Natürlich können aber auch andere Systeme angebunden werden, zum Beispiel Prozessleitsysteme, welche die Maschinendaten aufnehmen, analysieren und auch ansprechend visualisieren. Die Datensätze direkt aus der Maschine können zusätzlich mit weiteren Informationen ergänzt werden. Beispielsweise durch Umgebungsdaten, um ein Bild über die Gesamtsituation einer Anlage zu erzeugen. Dadurch lassen sich sehr effizient ganze Anlagenkomplexe überwachen und steuern.